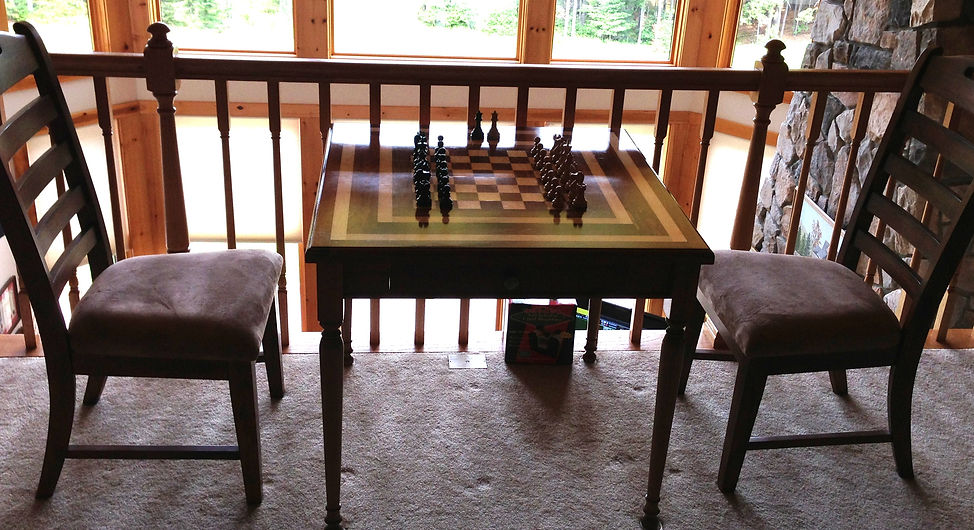
Chess Boards and Tables
Building a chess table was my first attempt working with hardwood. It was actually my first attempt at a number of things. Since I built this chess table, I've gone thru a lot of trial and error and mistakes to come up with ways and means that work for me. Please consider that as I describe how I built this table and excuse my dropping out of first person when I write about it. My descriptions of procedures are going to be less about how I built the first table and more about how I would build it now.
​
The wood I used for the chess table was Brazilian Cherry (Jatoba Wood) and Maple. I picked these two because their natural color provided enough contrast for the top of the chess table. I bought a bundle of 3/4" thick, 3.25" wide, unfinished wood flooring of each type (about 21 sq. feet per bundle) from Lumber Liquidators (the business is now named LL Flooring).
NOTE: I'm not sure exactly where the idea came from of using flooring from Lumber Liquidators (now LL Flooring), but I know I couldn't find, at that time or since then, a less expensive source for good quality hardwood.
​
As I started to build the top of the table, I planned to save myself some work by using most of the hardwood flooring in its originally configured shape which is tongue-and-groove edges and a smooth top and grooves on the bottom. I figured I could hide the grooves on the underside of the table. I made the top of the table a double thickness of wood, and I was able face the grooved sides of the wood together with the smooth side out. I also figured I could use the tongue-and-groove edges to put the wood together. Both of these time saving techniques sound good, but they're not. The tongue-and-groove doesn't provide the very tight, clean edge mating I was looking for so that didn't pan out, and having to hide the grooves is just too much of a pain to deal with. I used these techniques on my first table, but I never tried it again. From this point on, the first thing I did with the flooring was to plane the flooring to remove the grooves and run the boards thru the table saw to remover the tongue and groove edges. This changed the size of the wood from 3.25" x 0.75" to 2.78" and 0.625". Quick comment: I have learned to prefer building with 5/8" hardwood boards. It's plenty strong at that width and it reduces the overall weight of the furniture. There's not quite as much room for error with piecing together 5/8" wood vs 3/4" wood, but it's not that big a problem.
Another thing I learned about hardwood, don't plan on leaving mistakes to be fixed in the sanding process. It's very hard to make progress sanding hardwood, especially Brazilian Cherry. For example: Brazilian Cherry is 2690 on the Janko hardness rating, New England white pine flooring is 420, red oak flooring is 1290, and the common pine you'd find at Home Depot is 380. So, if you have ever sanded Home Depot pine, just imagine that this stuff is 7 times harder to sand. The lesson is, get it right when you first cut it, plane it, join it, or router it. That way, when you sand it, you won't give up, feed it to your fireplace while swilling beer, and watch the flames while they struggle to burn it up because it's so damn hard.
However, the fact that hardwood doesn't splinter like pine does and tends to provide cleaner cuts, rips and router cuts makes it the wood I prefer to work. The final product is also better if it's made from hardwood, and that is especially true if the wood in Brazilian Cherry.
​
During the time I was building my first table, I had a Shopsmith multitool. This tool could be used as a lathe which I planned on using to turn the legs of the table. Long story short, either the lathe wasn't very good, or I wasn't very good (that's my best guess), so gave up trying to turn the legs myself and ended up buying the legs online. They were about $20/leg and well worth not having to figure out how to use a lathe properly. ​​
​
How to make sure you rip a square edge
I'm going to start the "how I built the table" description by first explaining what I learned about ripping a perfectly square edge using a table saw so you can make clean, tight joints. And, just to let you know what I found out by painful experience, relying on the saw's angle adjustment or using a square are NOT good enough methods.
-
First, use a sharp blade. This can get to be an expensive requirement. I ended up buying a blade sharpening machine, but not before spending hundreds of dollars on saw blades over the years. This may be a llittle out of context, but my "how to's" all pretty much start with "use a sharp blade".
-
Make sure the table saw blade is exactly perpendicular to the saw table. Here's how:
-
Using your table saw's adjustment, move the blade to the zero degrees angle. That should be straight up and down.​ You can also use a small square at this point to get it as close as possible before the upcoming test.
-
Mark a scrap 12" long x 3" to 4" wide board with the following markings: Draw a line across the 6" point on the board, then write FST (front side top) on the upper 6" section of the board and FSB (front side bottom) on the lower section of the board. Turn the board over and write BST (back side top) on the upper 6" section and write BSB on the lower 6" section. I know it's a pain, but I've forgotten which side is which enough times to know it's worth the effort.
-
With the rip guide bar positioned to the right of the blade, rip a little of the edge of the 12" long piece of wood and mark the edge that was ripped on both sides so you know what side was ripped.
-
Cut the 12" board in half at the 6"inch line. Now it time to test the edge.
-
Keeping the front side up, put the two 6" boards together at the edge that was ripped. Make sure the boards are on a perfectly flat surface.
-
If there is a gap between the top edges of the boards, you'll have to tip the top of the blade to the left and rip the board again. You'll repeat this process until there is no gap.
-
Once there is no gap in the test above, turn the boards over to the back side, and put them together at the edge that was ripped. If you have a gap, you went a little too far adjusting the saw top to the left. Adjust the top of the saw blade back to the right slightly and rip the edge again.
-
Keep repeating the last two steps until there is no gap between the top of the ripped edge no matter how you put them together.
I started the build with the chess board in the middle, top of the table. The goal is to end up with 32 maple and 32 Brazilian Cherry (hereafter called BzC) alternating squares of exactly 2" each.
​
First prepare 8 pieces of wood, 4 maple and 4 BzC, at least 18" long and 2.25" wide. Make sure the ends are cut squarely (use the same kind of test on your miter saw I described above to make sure you are making square cuts). Also, at least one edge of the boards have been trimmed to make them perfectly square (again - see the procedure above).
​I then set my table saw to a rip width of exactly 2", and ripped a piece of scrap wood as a test, then I readjusted my saw again, and ripped another piece of scrap wood (repeating as often as needed) until finally I had ripped a piece of scrap wood exactly 2" wide.
​
I then ripped 3 maple and 3 BzC of the 8 19" boards i prepared earlier to a width of exactly 2.00"wide, and a length of 18" to 19". I then ripped 1 maple and 1 BzC boards 2.125" wide and 18" to 19" long (these will be the edge boards).
​
Using a Dewalt biscuit jointer (see right), I joined and glued together the six 2.00" wide boards (middle boards) alternating between wood types, and then joined and glued the two 19" 2.125 19" (the boards on the edges) to the assembled 6 board piece.
​​


NOTE: I try to take the time to clean off the excess glue with a damp (approaching wet) paper towel. I get as much of the excess glue off as I can because it's much easier to wipe wet glue off with a damp paper towel than it is to chisel or sand it off after it dries. Also, a paper towel rarely digs too deeply ruining a piece of wood as a chisel can.
​
Speaking of glue, I normally use the Titebond Premium glue shown to the right. The original (red label) tends to dry too fast when I'm putting together a lot of pieces at once. The Ultimate (green label) is overkill for furniture that is to be placed inside.
​​
After the glue dried, I cleaned up one edge where the glued pieces meet to use as a table saw guiding edge. NOTE: I always try to keep one end of the glued pieces exactly on edge so that one end of the assembled piece has a straight edge that I can use as the guide side on the table saw.
Then I ripped the 16.25" wide 19' long assembled piece so that I had eight 2.125" wide x 16.25" long pieces of alternating wood type every 2''. I then examined the pieces for correctable flaws, readjusted my table saw down to exactly a 2" rip width, tested the width by ripping a piece of scrap wood, and then ran six of the eight pieces thru the saw again. The two I didn't rip will be used as edge pieces below.
​
Now the 6 pieces that are exactly 2" wide are biscuit joined and glued together in the alternating pattern of a chess board, and the wider pieces are joined and glued to the six as the edge pieces. I now have the chess board together, but the edges still need to be trimmed down so that all the edge squares are exactly 2" to match the inside 36 squares. By leaving he boards with a little excess on all 4 sides, I could take my time and trim the edges in the table saw and get 64 - 2.00" squares on the chess table top.
I'm not sure there why I used the pattern I did from the chess board to the outer edge. I just kept adding strips until I had a table that was about 34" square.
One thing on the build that I was not happy with was the way I built the drawer slides. At this point in my furniture building, I decided I wanted everything made with wood. This included no drawer slides from Amazon. My opinion on this has changed because of the grief the wooden drawer slide on the chess table caused me. I made the slides out of BzC by cutting 1/4" grooves in long slats I attached to the drawer, and cutting matching grooves in the drawer supports. Idea sounds great but you need to provide a little slack in the size of the grooves. I've been sanding and oiling the grooves every year or so since I built it to keep the drawer opening smoothly.